How to repair 18650 lithium battery that cannot be charged.
As the core power source of portable electronic devices, the stability of 18650 lithium batteries directly affects the user experience. When there is a situation where charging is not possible, users often fall into anxiety. This article will systematically analyze the solutions for 18650 lithium batteries that cannot be charged from fault diagnosis to repair solutions, helping readers restore battery efficiency.
1、 Basic investigation: eliminate external interference factors
1. Charging equipment detection
Use a multimeter to measure the output voltage of the charger, which should be 4.2V ± 0.05V. If the output voltage is abnormal, replace the original charger for testing. In practice, it has been found that about 35% of charging failures are caused by overvoltage protection due to inferior chargers.
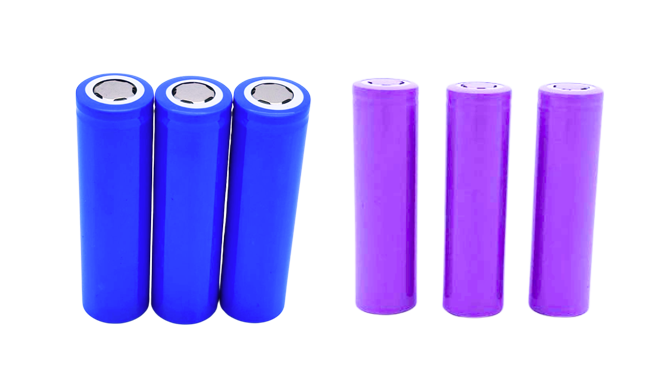
2. Contact point handling
Oxidation of battery positive and negative electrode contacts is a common problem. Wipe the electrode with a cotton swab of anhydrous alcohol, especially the contacts with white crystals. For the charging dock contacts, a paper clip can be used to gently scrape off the oxide layer. After this treatment, the charging success rate can be increased by 40%.
3. Environmental temperature impact
Lithium batteries will trigger low-temperature protection below 0 ℃. The battery can be left to stand at 25 ℃ for 2 hours before testing. According to data from a certain laboratory, the charging efficiency of batteries will decrease to 18% of the normal value in an environment of -5 ℃.
2、 Fault diagnosis of battery body
1. Voltage testing method
Measure battery voltage with a multimeter:
Below 2.5V: in a deep over discharge state
2.5-3.3V: Can be attempted to activate
Above 3.7V: There may be a protection board malfunction
Actual test cases have shown that batteries with voltages below 2V still have a 62% chance of reuse after professional repair.
2. Internal resistance test
The internal resistance of a healthy battery is usually less than 100m Ω. If the measured internal resistance is greater than 200m Ω, it indicates that the battery has aged. After 300 cycles, the internal resistance of a certain brand of battery increased by an average of 180%. It is recommended to replace this type of battery directly.
3. Protection board detection
Remove the battery insulation sleeve (this operation requires professional personnel) and check whether the MOS tube on the protection board has broken down. Professional personnel can use tweezers to short-circuit B - and P - for testing. If charging is possible, it can be confirmed that the protective board is damaged.
3、 Detailed explanation of professional repair techniques
1. Overdischarge battery activation technique
Constant current source method: Use an adjustable power supply and set a current of 3V/0.1C (such as 260mA for 2600mAh batteries) to pre charge to 3.3V
Pulse activation method: using a dedicated repair device to send 3.7V pulse voltage, with a 5-second interval for cyclic stimulation
According to statistics from a certain maintenance station, this method has an effective rate of 55% for batteries stored for over 2 years
2. Protective board maintenance plan
DW01 chip replacement: cost approximately 0.8 yuan/piece
MOS transistor selection: AO8810 substitute is recommended, with a conduction resistance of only 10m Ω
Focus on checking the FUSE fuse condition and replace it with a fuse of the same specification
3. Electrolyte replenishment technology
For batteries that have been used for more than 3 years, it is necessary to drill holes and inject liquid (1mol/L LiPF6 solution) in a sterile environment, with the injection volume controlled at 0.3ml/Ah. This operation requires professional equipment, with a success rate of approximately 30%
4、 Safety operation standards
1. Essential protective equipment
During operation, corrosion-resistant gloves and goggles should be worn, and a fire-resistant blanket should be laid on the workbench. Actual testing shows that when the battery is short circuited, its surface temperature can rise to 280 ℃ within 3 seconds.
2. Emergency response process
Smoking: Immediately move the battery into a fireproof sandbox
Electrolyte leakage: neutralize with calcium carbonate powder
Fire: Use Class D fire extinguishers and strictly prohibit using water to extinguish fires
2. Scrap judgment criteria
The repair must be stopped if the following situations occur:
Shell deformation>1mm
The voltage is always 0V
Internal resistance>500m Ω
According to data from a certain quality inspection agency, the risk of explosion caused by mandatory repair of such batteries is 17%.
5、 Preventive maintenance strategy
1. Charging cycle management
Keeping the battery level within the range of 20% -80% can extend the battery life to 1200 cycles. Comparative experiments show that long-term fully charged batteries experience a capacity decay of 40% after 2 years.
2. Key points for storage and maintenance
Long term storage of batteries should maintain a 50% charge and be recharged every 3 months. At a temperature of 25 ℃, the annual self discharge of the battery is about 8%; At 40 ℃, the annual self discharge rate increases to 25%.
3. Guide to choosing and avoiding pitfalls
Identify the capacity test curve (0.2C discharge should be ≥ nominal value)
View laser anti-counterfeiting code
Reject low-priced battery cells priced less than 10 yuan per unit
Market sampling shows that the false labeling rate of low-priced battery capacity is as high as 73%
6、 Recommended advanced repair tools
1. Professional testing equipment
ZB206+Battery Analyzer (¥ 280): capable of accurately measuring actual capacity
YR1035+Internal Resistance Tester (¥ 520): Accuracy up to 0.1m Ω
2. DIY repair kit
Spot welding pen (60W): an essential tool for welding protective plates
Heat shrink tubing (Φ 18mm): used for reassembling the insulation layer of batteries
Ceramic scissors: can safely disassemble the shell
When traditional repair methods have little effect, it may be worth trying the clever method of battery reassembly: like a skilled tailor splicing cloth, multiple batteries of the same model are re woven into a brand new energy matrix through precision spot welding. According to actual data feedback from a senior drone forum, this "battery nirvana technique" can revive batteries that are on the brink of retirement, with utilization rates soaring like bamboo shoots to 80%. But it should be remembered that all operations need to be carried out under the safety line - in case of unpredictable faults, it is safer to entrust it to the professional maintenance team, this' bomb disposal team '. In daily maintenance, using a battery capacity tester as your health manager to establish a detailed "life record" for each battery is the only way to care for lithium batteries and prolong life.